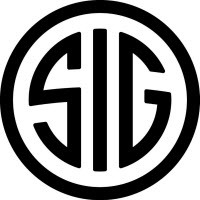
Description
Supervisor, Machine Maintenance
1st Shift
SIG SAUER, Inc. is a leading provider and manufacturer of firearms, electro-optics, ammunition, air guns, suppressors, remote controlled weapons stations, and training. For over 250 years SIG SAUER, Inc. has evolved, and thrived, by blending American ingenuity, German engineering, and Swiss precision. Today, SIG SAUER is synonymous with industry-leading quality and innovation which has made it the brand of choice amongst the U.S. Military, the global defense community, law enforcement, competitive shooters, hunters, and responsible citizens. Additionally, SIG SAUER is the premier provider of elite firearms instruction and tactical training at the SIG SAUER Academy. Headquartered in Newington, New Hampshire, SIG SAUER has over 3,200 employees across twelve locations in three states and is a certified Great Place to Work™. For more information about the company and product line visit: sigsauer.com.
Position Summary:
This Supervisor, Machine Maintenance leads the team of Machine Maintenance Technicians and Preventative Maintenance Technicians across all shifts and performs maintenance and repairs on all CNC equipment. The team's mission is to ensure the readiness of all manufacturing equipment and keeping machine downtime to an absolute minimum with emphasis on high volume, high precision, automated CNC equipment including horizontal machining centers, multi-spindle machining centers, CNC turning and mill turning equipment. Working both independently, and in a team environment, this supervisory position will collaborate with Production Supervision, and Managers.
FLSA: Non-exempt
Job Duties and Responsibilities:
- Inspect machine repairs to ensure that work performed meets SIG expectations of quality.
- Coordinate with production on the scheduling of downtime for repair and maintenance of equipment.
- Manage the execution of machine repairs including preventative maintenance.
- Monitor coolant maintenance for machining operations such as contaminant removal, coolant monitoring, and control.
- Create and maintain reports, metrics and key performance indicators related to machine downtime.
- Manage the record-keeping for all service and maintenance performed on the machinery.
- Follow all required safety practices associated with the specific practices associate with the specific job and follow safety procedures, security protocol.
- Manage spare parts inventory levels and track parts used for repairs.
- Ensure the Maintenance team is properly trained on their job duties and proper use of the Computerized Maintenance Management System (CMMS).
- Provide guidance and direction to the team.
- Keep Maintenance, Production and Operations Management informed of all machine status by daily reporting and attending meetings at a frequency determined by those entities.
- Interact with Production Supervisors to improve and maximize plant output, efficiency, quality, and safety.
- Interview, select and train new hires.
- Provide performance feedback including completion of employee performance appraisals and address employee concerns in an efficient and fair manner.
- Provide timely, clear and consistent feedback to all employees. Recognize and reward employees.
- Participate in 5s workplace organizational activities and maintain the area in good working order through sustainment activities, including requests for maintenance when needed for both personal space and multi-use department spaces.
Education/Experience & Skills:
- High School diploma or equivalent is required; Associate's degree in a related field is preferred, and a minimum of 10 years in a production machine maintenance role and 1-2 years of previous experience in leading a team.
- 10 years of experience with PLC controls in CNC milling or lathes; demonstrated proficiency on Fanuc or Siemens controls is required.
- Ability to accurately diagnose and repair machine problems to minimize downtime.
- Excellent troubleshooting skills and knowledge regarding electrical and electronics, and electro-mechanical assemblies and hydraulic and pneumatic repairs.
- Must be able to work on several projects at a time, to meet the needs of a rapidly changing environment.
- Proficient in the use of Microsoft Word, Excel and familiar with Microsoft PowerPoint. Proficient in the use of CMMS.
- Must be able to respond to and manage issues pertinent to the position after core business hours.
- Must be able to clearly, concisely, and accurately convey ideas and information to others, both verbally and in written form.
- Demonstrated ability to prioritize and manage multiple projects at once.
- Strong planning and team building skills.
Working Conditions:
- Regularly perform repetitive tasks.
- Work is primarily standing (90 + % of the shift) except for lunch and break periods.
- Shifts are 8 hours, 10 hours, and 12 hours.
- The duties of this job normally require exposure to a typical manufacturing environment. Frequent standing, sitting, stooping, squatting, walking, and stair climbing can be expected along with frequent lifting and/or moving of tooling, parts containers, and materials up to 40 pounds.
- Must be able to reach with hands and arms, bend and kneel frequently at a minimum of 50% of the shift, as well as undergo repetitive wrist, hand, elbow, shoulder, and ankle motions.
- Must demonstrate proficient fine motor skills, ability to grip, reach, pull, turn, and use tools to torque fixtures in various machinery or in the assembly, machining, or testing of parts.
- Specific vision abilities required may include close vision, distance vision, peripheral and depth perception, and the ability to focus on fine print.
- Must wear required Personal Protective Equipment (PPE) where required.
- Must comply with all work exposure EH&S training requirements and adhere to SIG SAUER Inc. security mandates.
SIG SAUER, Inc. provides equal employment opportunities to all employees and applicants for employment and prohibits discrimination and harassment of any type without regard to race, color, religion, age, sex, national origin, disability status, genetics, protected veteran status, sexual orientation, gender identity or expression, or any other characteristic protected by federal, state, or local laws.
Apply on company website