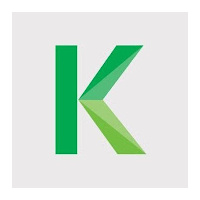
Description
Maintenance Engineer
Location: Weston, FL (near Miami and Fort Lauderdale, Florida (FL))
Function: Clinical and Commercial Manufacturing
Reports to: Director, Facilities and Engineering
Summary:
Responsible for maintenance and engineering activities in the context of pharmaceutical manufacturing equipment. The Specialist will be responsible for clinical/commercial manufacturing equipment including semi-automated to automated and large-scale manufacturing operations. The Specialist will utilize industry standard and novel equipment, processes, and methodologies to install, repair, and maintain equipment to standards of safety, quality, and availability. The Specialist will be responsible for developing, maintaining, and optimizing calibration and PM cycles for all manufacturing equipment. The Specialist will interface with Quality, Manufacturing and R&D teams and be responsible for independently providing direction, initiation, planning, coordination, implementation, execution, control, and completion of specific maintenance and repair of departmental equipment. This is a hands-on position which requires daily tactical responsibilities leading up to strategic decisions.
Essential Duties and Responsibilities
• Provide technical leadership to the manufacturing team and management.
• Lead and execute maintenance both repair and preventative.
• Responsible for developing and implementing best practices for maintenance and service in accordance with manufacturers recommendations.
• Develop, propose, and implement vision, strategy, policies, processes, and procedures to aid and improve business performance.
• Lead scale-up and commercialization efforts.
• Lead root cause investigations.
• Lead life-cycle management efforts.
• Lead and execute technical analyses including statistical analysis and tolerance analysis.
• Document studies and author documents per US FDA, EMA, MHRA and other global health authority requirements.
• Interface and lead activities with third party contract research, development, and manufacturing organizations.
• Ensure that manufacturing strategies and processes are in place to meet business objectives and operational needs in terms of price, quality, and delivery targets and that enable the organization to function and compete effectively in the market.
• Proactively evaluate the challenges faced by the business and take actions to mitigate risks and develop opportunities.
• Contribute towards and maintain device design history files (DHF).
• Document standard operating procedures (SOPs) for design controls and manufacturing in the context of pharmaceutical drug-device combination products.
• Contribute towards overall business strategy and annual budget process.
• Provide project updates/reporting through program governance.
• Provide leadership and support for inter-site best practices (technology transfer, process validation, etc.) and phase appropriate guidelines and policies.
• Execute project strategy, priorities, and milestones ensuring visibility and accountability.
• Proactively lead with integrity and engage cross functional project teams and stakeholders.
• Support organizational / departmental initiatives.
• Prepare and conduct presentations to all levels of the organization which may include project technical and budgetary information.
Qualification Requirements
• A B.S, in Mechanical Engineering, Electrical Engineering, Robotics or related discipline with 5 to 7 years, A.S. with 7 to 10 years' experience in pharmaceutical or related field.
• Experience with cGMP manufacturing in the context of pharmaceutical clinical and commercial manufacturing is a must to have.
• Must possess expert knowledge and experience with manufacturing and aseptic filling processes including manual, semi-automated and/or commercial scale automated processes.
• Experience with ComapctLogix (PLC); AVEA (formerly Wonderware); Windows 10 Enterprise IoT LTSB; PMS (Particle Monitoring Systems) software packages is highly preferred.
• Experience w/ Staubli robots is preferred.
• Proven automation experience with increased levels of responsibility
• Knowledge of GAMP lifecycle and quality management processes employed in the pharmaceutical sector.
• Must possess knowledge of various pharmaceutical processing equipment design, optimization, qualification, and life-cycle management.
• Must possess knowledge of regulations and standards including US 21 CFR Part 820, 821
• Experience with DCS and/or PLC software design.
• Experience in development of orally inhaled and nasal drug products (OINDPs) is a plus.
• Experience with IO/OQ/PQ's is a plus.
• Experience with FAT/SAT is a plus.
• Strong English language skills including writing ability and oral communication.
• Demonstrates good judgment as well as cultural, social, and environmental awareness.
• Trade background would be an advantage
• Good analytical & problem-solving skills
Salary Range: $100 – 130K
As part of our promise to talent, Kelly supports those who work with us through a variety of benefits, perks, and work-related resources. Kelly offers eligible employees voluntary benefit plans including medical, dental, vision, telemedicine, term life, whole life, accident insurance, critical illness, a legal plan, and short-term disability. As a Kelly employee, you will have access to a retirement savings plan, service bonus and holiday pay plans (earn up to eight paid holidays per benefit year), and a transit spending account. In addition, employees are entitled to earn paid sick leave under the applicable state or local plan. Click here for more information on benefits and perks that may be available to you as a member of the Kelly Talent Community.
Why Kelly® Engineering?
Your engineering skills are in demand, but how do you find the right fit? Easy. At Kelly Engineering, our team creates expert talent solutions to solve the world's most critical challenges. We connect you with leading organizations where you can collaborate on innovative projects, work with cutting-edge technologies and accelerate your growth. Whether you prefer the variety and flexibility of short-term projects or are looking for a long-term opportunity, we're here to guide you to the next step in your engineering career.About Kelly
Work changes everything. And at Kelly, we're obsessed with where it can take you. To us, it's about more than simply accepting your next job opportunity. It's the fuel that powers every next step of your life. It's the ripple effect that changes and improves everything for your family, your community, and the world. Which is why, here at Kelly, we are dedicated to providing you with limitless opportunities to enrich your life—just ask the 300,000 people we employ each year.Kelly Services is proud to be an Equal Employment Opportunity and Affirmative Action employer. We welcome, value, and embrace diversity at all levels and are committed to building a team that is inclusive of a variety of backgrounds, communities, perspectives, and abilities. At Kelly, we believe that the more inclusive we are, the better services we can provide. Requests for accommodation related to our application process can be directed to Kelly's Human Resource Knowledge Center. Kelly complies with the requirements of California's state and local Fair Chance laws. A conviction does not automatically bar individuals from employment. Kelly participates in E-Verify and will provide the federal government with your Form I-9 information to confirm that you are authorized to work in the U.S.
Apply on company website