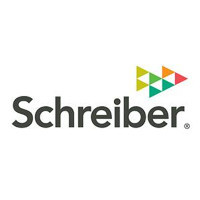
Description
Job Category: Quality Job Family: Plant Quality Assurance Job Description:
To provide leadership to the men working in the QC department and be accountable for their performances. To assess and monitor performances of partners working in the department.
What you'll do:
- To organize shift duty for all employees & allotment in respective shift of the section.
- To give release for all products on the basis of specification and customer requirement through Oracle system.
- To ensure that all testing done by the subordinates are as per Standard Operating Procedures.
- To verify quality records on routine basis. To ensure coordination with production for product quality feedback.
- Review & circulate new product formulation & specification to concerned partners.
- To provide customer complaint response.
- To give in house training to subordinates as and when required.
- To implement & follow the GMP & GLP requirements.
- To carry out sensory evaluation of products.
- To prepare COA of finished product.
- To carryout cleaning validation, allergen validation and any
- process validation as and when required
- Co-ordinate with production in case of any deviation in product.
- To raise indents for glassware's/chemical and other requirement for lab.
- To send samples to external lab and customer as per requirement.
- To comply with the requirements of Food safety Management Systems.
- To carry out any other job assigned by the seniors.
- To conduct Proficiency test of all analysts.
- To give conditional release prior to completion of inspection and testing in consultation with seniors / customers.
- Review HACCP plan & other ISO relevant document.
- Review action taken on non-confirming product & closure of NC. To participate in external audits.
- To conduct forward and backward traceability as per defined frequency and as & when required.
- Implementation of policies decided by the higher authorities. To comply with the requirements of EMS & OHSAS 18001.
- To set the safety goals and objective and ensure compliances with team support. To define, implement and maintain the compliances of safety rise initiative & inform team to comply the same.
- Set target of BBS, safety rise, JCC and safety audit score and track the outcome of the programs. Track, analysis and investigate the incidents.
- To review the HIRA & Aspect impact of section.
- Coordinate central safety committee and safety steering committee meeting
- Provide training to partners on OH&S management system. Log sheet verification
- RM / PM Challenges, Online Challenges Communication to relevant stakeholder
- To enter QPA data in system and circulate the reports to all concerned partners.
- Regular plant round & highlight deviations with concern team.
- Attend meetings & calls with internal & external team, Customers.
- Sensory / KQT of product as per requirement. Fulfill GLP requirements
- PDI observations share with team & follow up. Fulfill LIMS requirements
What you need to succeed:
- Bachelor's/ Master's Degree in Food Science, Dairy Technology, B.SC/ M. M.Sc. Chemistry, Microbiology or related field is required
- 10+ years' experience in Quality Assurance, Food Safety or Production
- Candidate shall have a sound knowledge of Quality control of milk and milk products, juice & Beverages. Well versed with the Food safety principles, HACCP and
- Proven leadership experience in a team environment
- Excellent interpersonal and problem-solving abilities (relationship building, teamwork, interpersonal insight, conflict resolution, customer orientation)
- ·Excellent Communication Skill (verbal communication, persuasive impact, listening, written communication)
- Judgment and thinking (strategic thinking, original thinking, judgment and decision making, problem solving, awareness)
- · Performance skills (accuracy with detail, planning and organizing, efficiency, business acumen)
- · Personal Characteristics (motivation/commitment, flexibility, assertiveness, develop orientation result orientation resilience, quality
- orientation)
Apply on company website